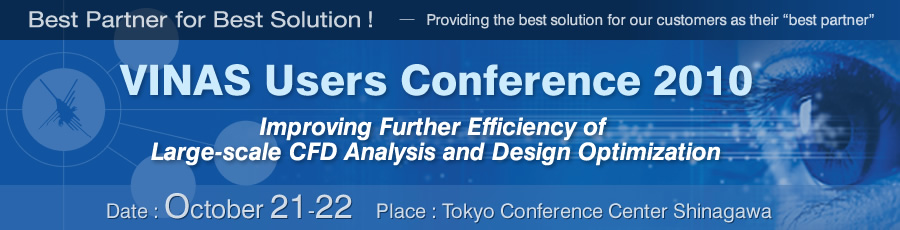
![]() |
||||
---|---|---|---|---|
![]() |
||||
Panel Discussion with Mr. Matthias Metschkoll from BMW and Mr.Peter Bohm from MAN Diesel & Turbo which receive high reputations in German industry which precedes in the field of weight reduction by structure optimization will be held. In the first section of this program, situations two German companies are facing are explained with a question-and-answer session afterward. In the second section, panel discussion with four German panelists and two Japanese panelists about weight reduction particularly technical issues necessary for vehicle design and development in the future will be held. The themes for this discussion will be decided based on the requests and questions that we collected from you when applying. |
![]() |
|||
Foreign panelists | ||||
![]() |
![]() |
|
||
Japanese Panelists | ||||
![]() |
![]() |
|
||
Developers of TOSCA, system for Structure optimization | ||||
![]() |
![]() |
|
||
13:30 - 13:35 | Opening: Greeting and explanation for the program |
|||
13:35 - 13:55 | [Section1] BPresentations on Weight reduction at BMW and MAN Diesel & Turbo, and Question-and-answer session
“New methods for multi-disciplinary shape optimization of a rear wheel carrier” Mr. Matthias Metschkoll, BMW “Topology Optimization for Lightweight Crankcase Design” Mr. Peter Bohm, MAN Diesel & Turbo |
|||
14:15 - 15:25 | [Section 2] Panel discussion on structure optimization and weight reduction, and Question-and-answer session with open discussion | |||
15:25 - 15:30 | Closing | |||
[Wanted: Discussion theme(s)] Theme(s) for this panel discussion will be decided based on your requests. Please send your requests for the topics or questions you would like to be discussed from online application for this panel discussion. |
* Registration will be required beforehand
* Entry/Leave is strictly prohibited once this session starts.
* Please note the program may change without prior notice.
* Company and product names are trademarks or registered trademarks.
![]() |
||||
---|---|---|---|---|
9:30 – 9:45 |
|
![]() ![]() |
||
9:45 – 10:15 | ![]() |
|
![]() ![]() |
|
Pointwise and Gridgen have unique capabilities for automatically handling poor quality CAD geometry, generating high-quality viscous meshes on complex geometries, and automating the meshing process with scripting. These techniques will be shown along with a preview of upcoming developments. | ||||
10:15 – 10:20 | Break | |||
10:20 – 11:00 | ![]() |
|
![]() ![]() ![]() |
|
Unfavorable wind conditions can cause the premature failure of wind turbine generators, thereby reducing business case certainty of a wind project. This session presents CFD activities at Vestas for risk mitigation in wind turbine micro-sitting. | ||||
11:00 – 11:15 | Break | |||
11:15 – 11:30 |
|
![]() |
||
11:30 – 12:00 | ![]() |
|
![]() |
|
In this presentation, the new features, functionalities and modules in TURBOdesignSuite 5.0 will be shown. The presentation will show how TURBOdesignSuite can be used throughout the design process for various turbomachinery components from preliminary design to multi-objective/multi-point design. | ||||
12:00 – 12:30 |
![]() |
|
![]() ![]() ![]() |
|
TURBOdesign-1 has been applied to design of turbine blade for wind-lens turbine which features "wind-lens" to concentrate wind on the turbine rotor to suit the wind conditions in Japan. | ||||
12:30 – 14:00 | Lunch / Demonstration | |||
14:00 – 14:20 |
|
![]() ![]() |
||
14:20 – 14:35 |
|
![]() |
||
14:35 – 15:05 | ![]() |
|
![]() ![]() ![]() |
|
In this presentation design optimization of fluid machinery will be discussed with the high fidelity CRUNCH CFD Multi-physics Framework. The design optimization framework uses evolutionary algorithms/Kriging method in conjunction with SCULPTOR for shape deformation while the different physics modules in CRUNCH CFD are used to compute the fitness functions. Applications considered include hovercraft lift fans, submarine sternplanes, and combustor cooling channels. | ||||
15:05 – 15:45 | ![]() |
|
![]() |
|
More efficient and reliable designs of rotodynamic pumps would yield major reductions in energy consumption maintenance costs. The adverse impact of separated and cavitating flows can be managed through CFD-aided fluid dynamical design. Variable geometry and rotative speed will meet changing system demands. New motor technology and controllability are key to reaping the benefits of these supposedly daunting design solutions. Examples illustrate the role of the fluids engineering community in the emerging generation’s inexorable march toward the greener and more productive environment of the future. | ||||
15:45 – 16:05 | Coffee Break / Demonstration | |||
16:05 – 16:35 |
![]() |
|
![]() ![]() |
|
In this application example, SCULPTOR’s mesh morphing function is used to accurately simulate complex vibration modes of aircraft structure in transonic flutter analysis. This new approach is also applied to the design of Mitsubishi Regional Jet, which is under development. | ||||
16:35 – 17:05 | ![]() |
![]() |
|
![]() |
JAXA is using CRUNCH CFD to apply high fidelity simulation to the new rocket engine research and development. An overview of its R&D activities will be presented in this session. | ||||
17:05 – 17:20 |
|
-Please note the program may change without prior notice.
-Company and product names are trademarks or registered trademarks.