 |
9:00 – 9:30 |
Registration |
9:30 - 10:10 |
- Concept of CCNV VECAMS
- Yasuhiko Fujikawa, President & CEO, VINAS Co., Ltd.
- Other than the internal servers, the use of external HPC servers is increasing in recent CAE/CFD analysis. We will be introducing the "CCNV", a VINAS-developed job aiding software that easily allows the use of multiple Linux servers with just the basic knowledge of Windows, and "VECAMS" our application operation contract services.
|
      |
10:10 - 10:50 |
- Introduction and demonstration of CCNV V1.4, VECAMS and V-SaaS.
- Kenji Morimoto, CCNV Development Group, Project Development Department, VINAS Co., Ltd.
- We will demonstrate the features of CCNV which strongly support the usage of HPC server of design process, and also introduce the new features and services, VECAMS and V-SaaS, to realize the cloud operations for open source applications.
|
   |
10:50 - 11:00 |
Coffee Break |
11:00 - 11:40 |
- Industrial use of FOCUS supercomputer and expectations for CCNV
- Dr. Takeshi Nishikawa
Supercomputing Professional, Foundation for Computational Science
- FOCUS, a supercomputer dedicated for industrial use, started its service with a computational capability of 22 TFLOPS in April 2011 and has been upgraded to have a twelve times faster speed of 272 TFLOPS in January 2014. Past and current usage of FOCUS will be reported in this presentation. In addition, expectations for CCNV, by which the FOCUS supercomputer can be seamlessly used from a Windows environment, will be discussed.
|
  |
11:40 - 12:05 |
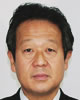 |
- Sponsor presentation
Fluid analysis by moving particle simulation method using GPGPU
- Mr. Hiroshi Kawakami
Corporate Officer,Responsible for Sales, Prometech Software, Inc.
|
  |
In recent years, computer technology using accelerator such as GPGPU has evolved rapidly. Along with it, a new simulation technique called particle method (MPS method) has been started to impact on the industry. Furthermore various application examples of MPS method are presented. |
12:05 - 12:35 |
- Consulting services for telecommunication and security using cloud services in CFD.
- VINAS, Chief consultant in charge of ICT and security
Masakazu Maruo
- In view of recent information security environment, the efficient use of the cloud services has become a vital theme in CFD/CAE. We will show effective measures and solutions for the use of mobile devices.
|
|
12:35 - 14:05 |
Lunch / Demonstration *Short presentation |
14:05 - 14:35 |
- Introduction of high-performance computing consulting service
- Naoyuki Sogo, High Speed Computation Technology Group, Project Development Department, VINAS Co., Ltd.
- We will introduce our HPC consulting service which is based on the development experience of the hi-speed and robust matrix solver SMS over the years.
|
  |
14:35 - 15:15 |
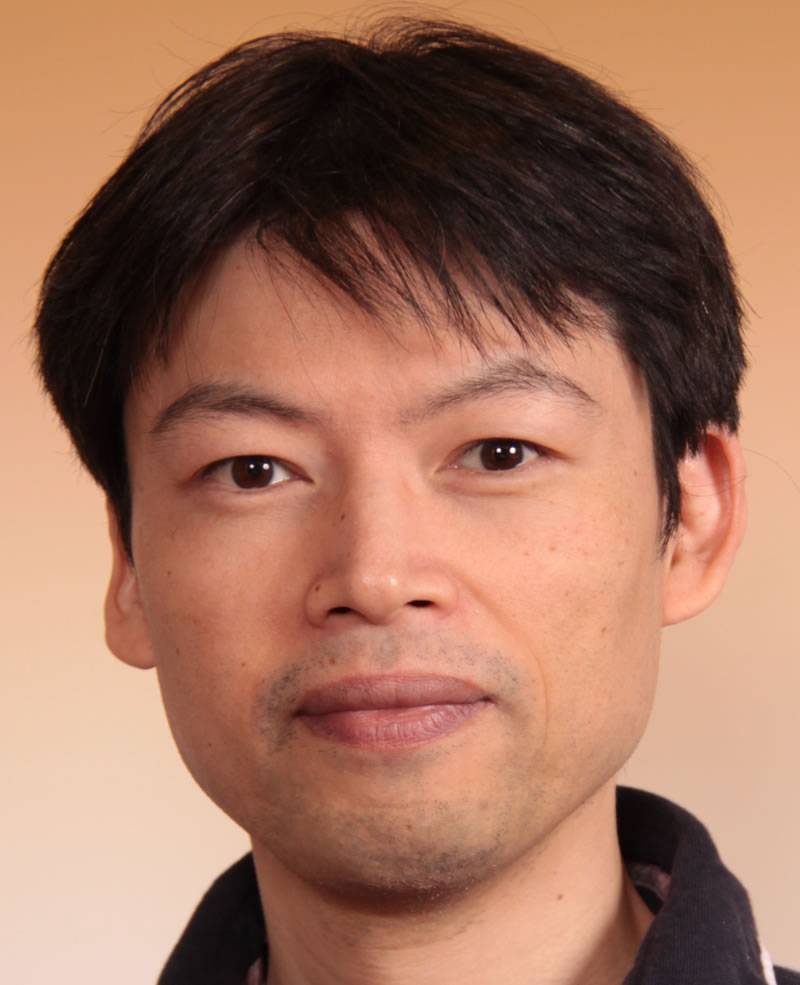 |
- NTChem: Software package for molecular electronic structure calculation
- Dr. Takahito Nakajima
Team Leader, Computational Molecular Science Research Team, RIKEN Advanced Institute for Computational Science
|
  |
I will introduce a newly developing software package for the molecular electronic structure calculation named NTChem. NTChem is designed for high performance on a computer with many compute nodes. |
15:15 - 15:35 |
Coffee Break/Demonstration *Short presentation |
15:35 - 16:15 |
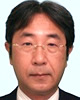 |
- Use of SMS in plastic extrusion CAE
- Ph.D. Shinichiro Tanifuji
President, CTO, Hyper Advanced Simulation Laboratory CO., LTD.
|
    |
In HASL, we have been developing commercial available CAE software for the polymer extrusion process. In the presentation, we will report about the collaboration of our products with VINAS’s Super Matrix Solver and
illustrate some application examples. |
16:15 - 16:55 |
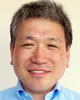 |
- Droplet shape analysis and visualization
- Dr. Yasuhiro Mizobuchi
Senior Researcher, Numerical Simulation Research Group, Institute of Aeronautical Technology, Japan Aerospace Exploration Agency
|
   |
Atomization of liquid jet is a critical process for the propulsion systems of aerospace vehicles. We conducted a large-scale simulation of the primary breakup process of a liquid jet and studied the shapes of droplets acquired by the simulation by using three parameters. The results were visualized as a distribution of droplets in the 3D parametric space by using FieldView. |
16:55 - 17:10 |
- (Broadcasting) Closing Speech
- Yasuhiko Fujikawa, President & CEO, VINAS Co., Ltd.
|
-Please note the program may change without prior notice.
-Company and product names are trademarks or registered trademarks.
 |
9:00 – 9:30 |
Registration |
9:30 - 9:45 |
- High Speed Computation Compressible CFD Solver V-FaSTAR 1.0
- Takeru Fukuchi, General-purpose CFD Group, Engineering Department 1, VINAS Co., Ltd.
- JAXA has developed a high speed computation CFD solver, FaSTAR. V-FaSTAR is a product in which VINAS added useful functions based on FaSTAR. V-FaSTAR has two main features; One is that the reliability of the CFD solver is high and the solver computation is fast. Another is economical efficiency. The licensing fee is not dependent on the number of jobs and the parallel number. The features and application examples of V-FaSTAR are introduced in the presentation.
|
    |
9:45 - 10:25 |
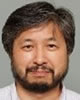 |
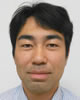 |
- Development of a highly efficient fluid solver “FaSTAR” pursuing the world's fastest compute speed
- Dr. Yuichi Matsuo, Head
Dr. Atsushi Hashimoto, Researcher
Numerical Simulation Research Group,Institute of Aeronautical Technology,
Japan Aerospace Exploration Agency
|
   |
FaSTAR (FAST Aerodynamic Routines) is a fast CFD code using unstructured mesh and consists of software tools for pre-processing, solving and post-processing. One of its main features is its high speed, achieved by incorporating a simple data structure, sorting of data for efficient memory access, parallelization by domain subdivision and convergence acceleration by the multigrid method. The presentation provides a technical overview of FaSTAR. |
10:25 - 10:40 |
- TURBOdesign Suite 5.2.3 promoting centrifugal compressor and turbocharger design
- Yukihiro Yamamoto, Turbomachinery Group, Engineering Department 1, VINAS Co., Ltd.
- The main new features in the latest version TURBOdesign Suite 5.2.3 are related to meridional design for radial inflow turbine, asymmetric volute design with compressible flow so that it become more useful mainly for centrifugal compressor or turbocharger design. The latest topics will be shown along with future development plans.
|
 |
10:40 - 11:20 |
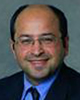 |
- Multidisciplinary Design optimization of High Performance Turbochargers by TURBOdesign Suite
- Prof. Mehrdad Zangeneh
Managing Director, Advanced design Technology
|
   |
In this presentation the application of different components of TURBOdesign Suite to design high performance centrifugal compressors and radial and mixed flow turbines for heavy duty duty diesel, Marine and gasoline engine applications will be highlighted. |
11:20 - 12:00 |
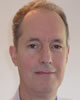 |
- An integrated approach to Centrifugal Pump Design and Qualification
- Mr. Brian Millward
Director of Technology, SPX ClydeUnion Pumps
|
 |
The range and versatility of the Centrifugal Pump continues to evolve, and by using the latest TURBOdesign inverse-design software from ADT, Engineers now have the opportunity of adding a further step change in performance to this surprisingly complex product. The presentation will show how an integrated approach to the design and qualification process can pay dividends. |
12:00 - 12:30 |
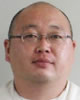 |
- Improvement of efficiency of pressure fan by TURBOdesign
- Mr. Takeshi Matsumoto
Research & Development Section, TERAL INC.
|
  |
In recent years, we have been facing increasing demands for high-efficiency products and new approaches are necessary to achieve an even higher level. The presentation includes our use of TURBOdesign to improve efficiency of a pressure fan based on an inverse solution method. |
12:30 - 13:50 |
Lunch / Demonstration *Short presentation |
13:50 - 14:05 |
- SCULPTOR V3.6, to improve work efficiency for shape optimization with large data size
- Yukihiro Yamamoto, Turbomachinery Group, Engineering Department 1, VINAS Co., Ltd.
- SCULPTOR V3.6 greatly enhances the speed and resources of the server machine by the new functionality “Sculptor Server”, which calls their features through the network. The latest features of Sculptor, improving work efficiency for shape optimization using large data, are shown in the presentation.
|
 |
14:05 - 14:45 |
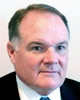 |
- A review of SCULPTOR’s latest new features, capabilities, and applications
- Mr. Phillip Belnap
President, Optimal Solutions Software, LLC
|
   |
New exciting applications of Sculptor’s shape optimization will be shown including the optimization of automobile aftermarket parts such as the rear wing for the Nissan GTR. A discussion of the OpenFOAM CFD model creation and solution (on the Cloud), defining the shape change variables, and using Sculptor’s Optimization Control Center to perform the shape optimization. The latest features in Sculptor V3.6 will be introduced, including improvements to Shape Matching, additional import/export interfaces to Autodesk SIM CFD, LSDyna, CRUNCH, and others codes, a new powerful Sculptor Server where Sculptor’s features can be called via network communication with library calls from a client software program, thus allowing any program to incorporate any of Sculptor’s features into their tools. |
14:45 - 15:15 |
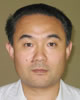 |
- Design shape optimization of HVAC by using SCULPTOR
- Mr. Akira Sakano
Lead Engineer, R&D Division. Fundamental Technology Research Dept. Analysis Technology Group, SANDEN CORPORATION
|
   |
This presentation provides an overview of an example in which SCULPTOR was used in shape optimization for HVAC. In order to achieve an objective of having a uniform velocity through an evaporator, the optimal shape was searched for by using a response surface based on the latin hypercube sampling method for evaluation of effects of design variables. |
15:15 – 15:25 |
Coffee Break/Demonstration *Short presentation |
15:25 - 15:45 |
- Introduction of CFD Suite Helyx-SAS 2.1 Improved based on OpenFOAM®
- Takeru Fukuchi, General-purpose CFD Group, Engineering Department 1, VINAS Co., Ltd.
- Helyx-SAS is a GUI for supporting the application of OpenFOAM® to design work. By direct connection with Pointwise, calculation convergency and analysis accuracy is improved. The solver is based on OpenFOAM®. The advantage of the solver is the function improvement such as boundary condition, and quality control by debugging etc.
|
   |
15:45 - 16:25 |
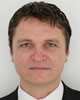 |
- Introducing HELYX
- Dr. Eugene de Villiers
Managing Director, Engys Ltd.
|
   |
HELYX is a new CFD suite based on Open Source technology. In this talk we introduce the technology and the framework that supports it. The code consists of a modern GUI that controls an open source solver suite. In addition, the suite supports a plug-in module framework that brings advanced and specialized capabilities to the platform. Modules include coupled solver, adjoint optimization, ship hydrodynamics and several other specialized components. |
16:25 - 16:55 |
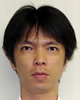 |
- Turbomachinery related equipments CFD using open source tools
- Dr. Shigeyuki Tomimatsu
Research Group Leader, Research and Development Center DMW Corporation |
       |
Open source CFD tools are becoming increasingly popular, but there are issues such as their lower robustness than general purpose CFD tools. Their performance including convergence property was studied by using different mesh models.
|
16:55 - 17:10 |
- Closing Speech
- Yasuhiko Fujikawa, President & CEO, VINAS Co., Ltd.
|
-Please note the program may change without prior notice.
-Company and product names are trademarks or registered trademarks.