 |
10:00 - 10:30 |
- Utilization Strategies of CAE/CFD in the Era of Cloud Computing
- Yasuhiko Fujikawa, President & CEO, VINAS Co., Ltd.
|
10:30 - 10:45 |
- Introduction of the latest FieldView making the visualization more efficient by means of “XDB Workflow”
- Shinya Higaki, CFD Product Group, Engineering Department 1, VINAS Co., Ltd.
- Both the reduction of visualization throughput time and the reduction of data size can be achieved by using the data management concept “XDB Workflow” provided by FieldView. The concepts and the case studies of XDB Workflow, and the features of the latest FieldView will be presented.
|
 |
10:45 - 11:25 |
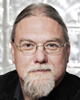 |
- CFD Post-processing at Any Scale: FieldView Strategy for Ultra-scale Visualization
- Mr. Steve M. Legensky
Founder & General Manager, Intelligent Light
|
 |
Intelligent Light has been working on a strategy that combines the ease of use and reliable performance of FieldView with visualization technology that scales to hundreds of thousands of cores. Although today's engineers use far fewer processors, future computers will make it easier to harness many more cores. Providing a reliable and open architecture for this future is vital to both the developers of ultra-scale codes and to the end users of analysis. |
11:25 - 11:30 |
Break |
11:30 - 12:10 |
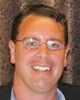 |
- Visualizing and Analyzing Very Large Simulation Data
- Dr. Hank Childs
Computer Systems Engineer, Visualization Group, Computational Research Division, Lawrence Berkeley National Laboratory
|
  |
Visit is a popular open source tool for visualizing and analyzing data. It owes its success to its three foci of increasing data understanding, large data support, and providing a robust and usable product, as well as its underlying design that fits today’s supercomputing landscape. In turn, this has led to hundreds of thousands of downloads, an R&D 100
award, and many customer success stories. In this talk, Hank Childs (architect of VisIt) will give an overview of the tool, how it deals with large data, and describe a few of its success stories. Further, he will discuss upcoming challenges stemming from changes in supercomputer architecture and the plans for dealing with these challenges. |
12:10 - 13:30 |
Lunch / Demonstration *Short presentation |
13:30 - 14:00 |
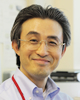 |
- Multi Purpose Optimization of High Speed Water Jet Propulsion Vessel Using CFD
- Professor Yusuke TAHARA
CFD Research Group, Fluids Engineering Department, National Maritime Research Institute
|
|
In this presentation, achievements of an international joint research supported by the Maritime Research Institute of the United States will be introduced. In the research project, single purpose and multipurpose optimization studies of single hull and multiple hull high speed vessels with water jet propulsion system are conducted. Through experiments, it has been verified that more than 5% of reduction in horse power has been achieved so far. |
14:00 - 14:30 |
|
- Automatic Grid Generation Algorithm for a class of 10 Billion and Visualization of its CFD computation
- Dr. Kenji Ono
Advanced Visualization Research Team , Advanced Institute for Computational Science(AICS), RIKEN
|
|
We developed a simulation system which can highly utilize the capacity of large-scale computing resource and achieves short turn-around time in all processes of simulations. An outline of an automatic grid generation algorithm which can generate a large-scale grid without manual operations will be presented, in addition to examples of simulations and visualization of results. |
14:30 – 14:45 |
- Pointwise V17.0 – Improvement of High-Quality Mesh Generation Functions
- Masanori Hashimoto, CFD Product Group, Engineering Department 1, VINAS Co., Ltd.
- The latest version of Pointwise V17.0 has included great features such as T-REX and Native CAD Readers. With these new features, high-quality mesh can be generated more robustly with saving your time. This presentation will provide an overview of Pointwise V17.
|
 |
14:45 – 15:25 |
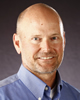 |
- Efficiency Improvements in CFD Meshing with Pointwise: Anisotropic Tetrahedra, Native CAD Import, and More
- Dr. Richard J. Matus
Vice-president, Sales & Marketing, Pointwise, Inc.
|
|
Due to recent Pointwise enhancements, meshes that used to require weeks to construct can now be built in minutes. Details of the major features that make this possible well be discussed and demonstrated. |
15:25 – 15:40 |
Coffee Break/Demonstration *Short presentation |
15:40 – 16:20 |
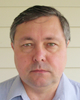 |
- Using Pointwise and Star-CCM+ In Design and Development of State-of-the-Art Centrifugal Compressors
- Dr. Mikhail Grigoriev
Senior Aerodynamic Engineer, Aero Engineering, Cameron, Compression Systems
|
|
This presentation focuses on challenges in design and development of the state-of-the-art high-performing industrial centrifugal compressors, including automated mesh generation in Pointwise for inlets, impellers, diffusers and volutes. We also discuss Cameron’s experience in using Star-CCM+ for advanced CFD analyses of centrifugal stages. |
16:20 – 16:50 |
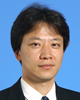 |
- Special Speech
Industrial Applications of Large-scale Large Eddy Simulation Using Front Flow/blue
- Professor Chisachi Kato
Director, Center for Research on Innovative Simulation Software, Institute of Industrial Science,The University of Tokyo
|
|
Front Flow/blue (FFB) is a general-purpose flow solver. It computes fine eddies in a turbulent boundary layer, and thus is expected to achieve the same level of accuracy that direct numerical simulation (DNS) does. Application examples of FFB to various kinds of flow-related products including cars, ships and turbomachinery will be presented. |
16:50 – 17:00 |
Break |
Keynote Speech |
17:00 – 18:00 |
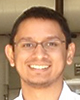 |
- High Performance Cloud Computing – The New Face of HPC
- Mr. Khawaja Shams
NASA's Jet Propulsion Laboratory.
|
  |
Is Cloud a suitable venue for HPC? The NASA Jet Propulsion Laboratory has been venturing into the cloud world over the last four years to evaluate its efficacy for high performance computing. We present the results of our benchmarks, where cloud computing makes sense, and case studies from NASA on cloud computing. |
Reception Party |
18:00 – 20:00 |
- Please join! This is a good opportunity for sharing and exchanging information with each other.
- - Venue: Tokyo Conference Center Shinagawa - 5th floor foyer [in front of the grand hall] -
*Please notify your attendance at the time of registration. |
-Please note the program may change without prior notice.
-Company and product names are trademarks or registered trademarks.
 |
10:00 - 10:30 |
- (Broadcasting)
Utilization Strategies of CAE/CFD in the Era of Cloud Computing
- Yasuhiko Fujikawa, President & CEO, VINAS Co., Ltd.
|
10:30 – 10:55 |
- To achieve short-term weight reduction and increase safety by TOSCA
- Hidetoshi Takaoka, Manager, Engineering Department 3, VINAS Co., Ltd.
- For weight reduction and improved safety, the establishment of the use of optimization tools and know-how is very important.
In this session, we will introduce the structural optimization system TOSCA and our structural optimization consulting services by our engineers from automobile and aircraft manufacturers.
|
 |
10:55 – 11:35 |
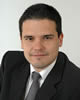 |
- Overview of new functionalities of the next TOSCA Structure version 7.2
- Mr. Chavdar GEORGIEV
Product Manager, International Presales, FE-DESIGN GmbH Germany
|
 |
FE-DESIGN, the technology leader in topology, shape and bead optimization, introduces the latest and updated product information of TOSCA Structure version 7.2. Besides the improvements on the existing features like advanced manufacturing constraints, support of nonlinearities and fatigue-based optimization many new innovative functionalities will be presented. |
11:35 – 12:15 |
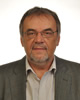 |
- Reduction of component weight in Aircraft and Automotive Industry by using TOSCA shown on industry examples
- Mr. Manfred Fritsch
Business Development, FE-DESIGN Germany and USA
|
 |
Decreasing component weight while achieving same or better performance in terms of stiffness and durability is a primary goal in the Aerospace industry. Reduced component weights result in lower fuel consumption and higher cargo and passenger capacities. Traditional design techniques fall short of achieving these goals due to time consuming nature of the design-analyze-modify cycle. Free optimization techniques such as Topology and Shape Optimization provide optimal initial designs and significantly reduce the engineering time. (Courtesy Goodrich) |
12:15 - 13:25 |
Lunch / Demonstration *Short presentation |
13:25 – 13:55 |
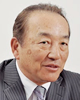 |
- Sponsor presentation
An introduction of nonlinear optimization technology based on Marc nonlinear general purpose FEA software.
- Dr. Motoharu Tateishi
Senior Director, Business Development, MSC Software Ltd.
|
 |
As the technique of optimization of a product performance especially although optimization technology has evolved, in recent years, its trial which applies an optimization technique not only to optimization of a linear problem but to a nonlinear problem is increasing.
In this lecture, several examples of the optimization which used Marc will be introduced.
|
13:55 – 14:45 |
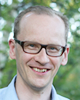 |
- With TOSCA Structure on the road towards a Simulation Driven Product Development Process
- Dr. Mikael Thellner
Technical Manager, Axle Development, Scania
|

|
The product development process at Scania has been driven by physical testing. In some areas simulations have replaced testing but in other areas the development process still relies on testing. At Scania we have started the journey towards a simulation driven product development process. |
14:45 – 15:00 |
Coffee Break *Short presentation |
15:00 – 15:30 |
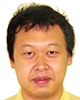 |
- Development of Car Body of CX-5 and Topology Optimization of Front Floor
- Mr. Masamitsu Tanaka
Staff Manager, Body Technology Development Gr. Body Development Dept., Mazda Motor Corporation
|
  |
In the development of the car body of CX-5, we set high goals in reduction of weight, achievement of world-class safety and high rigidity, and realizing flexible manufacturing. This presentation will show how we achieved these goals and include examples of framework designs evaluated in the early stage of development using TOSCA. |
15:30 – 16:00 |
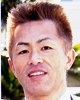 |
- Application of Non-parametric Optimization Technology in the Development of Multifunction Peripheral
- Mr. Atsuhiko Shimoyama
Functional Device R&D Division Product Elements R&D Center, Konica Minolta Business Technologies, Inc.
|

|
The reduction of weight is becoming ever more important in the development of Multifunction Peripherals. This is in order to lower its costs as well as the impact on the environment. To achieve this goal, we have introduced the non-parametric optimization tool TOSCA in the development of our Multifunction Peripherals. In this presentation we will give a brief explanation of the project which includes:
1.An explanation of the research that was made for the introduction of the software.
2.Several examples to illustrate how the program has been used after its introduction.
3.The particular conditions that must be considered for the use of the Tosca software.
|
16:00 – 16:15 |
- New features on OOFELIE::Multiphysics V4.4, the strong coupling simulation system for industry designers
- Sadahiro Kan, Fluid Design Optimization Group, Engineering Department 2, VINAS Co., Ltd.
- The new features of OOFELIE::Multiphysics V4.4 which can simulate the strong coupling behavior between structure, thermal, electric, fluid and so on, will be presented. The new functionalities for MEMS device simulation, and the latest case studies of thermo-mechanical simulation and fluid structure interaction simulation will be also provided.
|
 |
16:15 – 17:00 |
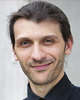 |
- Recent trends in multiphysics simulations using OOFELIE::Multiphysics
- Mr. Pascal De Vincenzo
General Manager, OPEN ENGINEERING
|
 |
OOFELIE::Multiphysics, the numerical simulation solution developed and commercialized by Open Engineering is used by industrials to predict the behavior of their systems. In the framework of this presentation, the accurate modeling of recent applications will be presented: sonar, LED, energy harvesting system, segmented mirror. |
(Broadcasting) Keynote Speech |
17:00 – 18:00 |
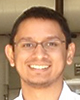 |
- High Performance Cloud Computing – The New Face of HPC
- Mr. Khawaja Shams
NASA's Jet Propulsion Laboratory.
|
  |
Is Cloud a suitable venue for HPC? The NASA Jet Propulsion Laboratory has been venturing into the cloud world over the last four years to evaluate its efficacy for high performance computing. We present the results of our benchmarks, where cloud computing makes sense, and case studies from NASA on cloud computing. |
Reception Party |
18:00 – 20:00 |
- Please join! This is a good opportunity for sharing and exchanging information with each other.
- - Venue: Tokyo Conference Center Shinagawa - 5th floor foyer [in front of the grand hall] -
*Please notify your attendance at the time of registration. |
-Please note the program may change without prior notice.
-Company and product names are trademarks or registered trademarks.